El taladro magnético portátil MAB 485 corta a través de Boeing 747
Con Big Imagination vienen grandes sueños y desafíos inesperados para lograr lo que la mente visualiza. Sólo los agujeros se interponen en el camino …
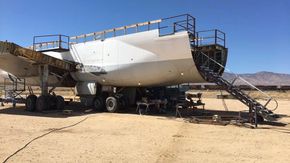
Big Imagination se acercó a CS Unitec para ayudarlo a especificar y suministrar un taladro y lubricante para cortar orificios en las vigas de titanio de un Boeing 747. Después de describir su visión, un proyecto de arte diferente a cualquier otro intento anterior, estábamos intrigados y emocionados. Esta es la historia del proyecto 747 y cómo CS Unitec y Big Imagination colaboraron para perforar 232 (sí, ¡doscientos treinta y dos!) Orificios de 5/8 "de diámetro a través de titanio de grado aeroespacial de 2" de espesor.
Este proyecto también apareció en thefabricator.com con derivaciones adicionales del proyecto, incluido su debut en Burning Man. |
El cerebro detrás de Big Imagination había estado soñando con convertir un avión en una pieza de arte de instalación móvil más grande que la vida durante casi 10 años. Hace años, Ken Feldman, CEO de Big Imagination, asistió a Burning Man, donde se encontró con una bicicleta tipo torpedo hecha con tanques de combustible para aviones. Su mente corrió con pensamientos de cuán impactante e innovador sería convertir un Jumbo Jet en una obra de arte móvil gigante, un proyecto nunca antes intentado.
Después de localizar a un Boeing 747-300 retirado en 1985 en el puerto de Mojave Air y Space Port y reunir a un ejército de más de 500 voluntarios para convertir su sueño en realidad, Feldman estaba en camino.
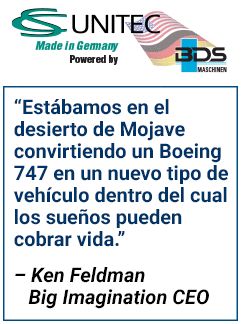
Para transportar el 747 a más de 500 millas de Mojave California a su destino final en el Desierto de Black Rock de Nevada, sería necesario modificarlo significativamente. La cola y una gran parte de las alas se retiraron, reduciéndola a 135 pies de largo, 32 pies de altura y 60 pies de ancho. Para moverse en autopistas públicas, tendría que dividirse en partes más pequeñas, dos secciones superiores del fuselaje y una sección larga principal del fuselaje inferior. El problema principal era el ancho de 60 'del fuselaje. Las alas y el tren de aterrizaje conectado debían retirarse de tal manera que se pudieran volver a colocar rápidamente en el sitio y aún así mantener su integridad estructural original.
La única vez que se retiraron las alas de un 747 y luego se las volvió a unir de esa manera fue en el 747 avión de transporte del transbordador espacial en exhibición en el Centro Espacial Johnson / Centro Espacial de la NASA en Houston, TX. Esta operación fue realizada por la unidad de operaciones de aviones de élite de Boeing en tierra.
La estructura de la columna vertebral de las alas y el tren de aterrizaje del avión es una enorme viga en I del tren de aterrizaje de titanio, "la mayor forja de titanio hecha en el hemisferio occidental", según Feldman. El equipo de Big Imagination viajó al Centro Espacial Johnson para inspeccionar el trabajo de Boeing. La eliminación de la viga I del tren de aterrizaje es esencialmente imposible. Boeing cortó la viga en I por la mitad y luego usó una serie de placas de empalme de titanio para volver a montar la estructura.
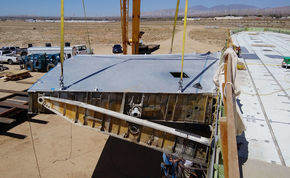
Feldman ahora sabía que era posible cortar y volver a montar la viga. El equipo de ingeniería de Big Imagination elaboró los cálculos para usar las placas de empalme de aluminio de la serie 7000 en lugar de titanio, ahorrando más de $ 50,000 en costos de materiales. El único problema en el plan era que la viga I no era solo de titanio ... era una aleación de titanio de grado aeroespacial. No tenían idea de cómo Boeing perforó todos esos agujeros en la viga en I.
La perforación a través de titanio presenta sus propios desafíos: el material tiene una relación resistencia / peso muy alta, no es ferroso y es resistente a la corrosión química y química. Además, el titanio tiene una conductividad térmica baja, así como una tendencia a adherirse a la herramienta de corte. Ambas complicaciones requieren equipo pesado y una gran cantidad de lubricante / refrigerante para perforar de forma limpia y evitar la falla prematura de la herramienta. Dicho esto, cuando la mayoría de los fabricantes prevén la perforación de titanio, se supone que se requieren equipos grandes y costosos, como el EDM de alambre y las máquinas de chorro de agua.
El equipo de Big Imagination estaba compuesto por miembros con una amplia variedad de experiencia, por lo que los cerebros para completar el proyecto no fueron un problema. El mayor obstáculo era que el equipo no tenía acceso a un área con control ambiental y todos los fabricantes de equipos originales de equipos de alta tecnología especializados, como Boeing, están disponibles para completar trabajos a especificación. Así que tenían que trabajar con herramientas eléctricas especializadas, más fabricación práctica e ingenio a la antigua usanza.
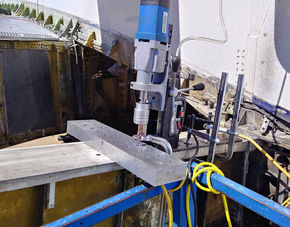
Después de clavar los puntos de corte, diseñar las placas de empalme y revisar tres veces los detalles, el equipo estaba listo para perforar.
El principal "perforador" de Big Imagination, el fabricante voluntario Keru McKenzie, tuvo la tarea de cortar los 232 orificios en la viga de titanio. El proceso que creó fue para taladrar previamente los orificios en las placas de empalme de aluminio de 7 "de espesor de la serie 7000, luego colocarlas en la viga de titanio I con una placa de acero de ½" de espesor (vea el diagrama a la derecha). Inicialmente, el equipo probó dos opciones para perforar los orificios, un taladro de mano y un taladro magnético de otro fabricante, y ninguno de los dos pudo "cortarlo".
Ahí es donde CS Unitec llegó a la escena. Feldman se contactó con nuestro equipo técnico para conocer cómo podían cortar primero un agujero a través del material apilado y luego repetir la acción 231 agujeros más. Se determinó que la mejor opción de perforación para el trabajo sería el taladro magnético portátil MAB 485. Con un máximo de 4-1 / 2 "de material variado para perforar en una sola pasada, el potente motor y la carrera larga del 485 parecían un buen ajuste. Su motor de velocidad variable de 2 marchas (50-250 RPM y 100-450 RPM) ofreció las bajas velocidades y el alto par de torsión que requería el trabajo. "Una de las mejores cosas de este ejercicio de magia es que tiene un gran lanzamiento", comenta Feldman. "Que es básicamente la única forma en que podríamos lograr esto".
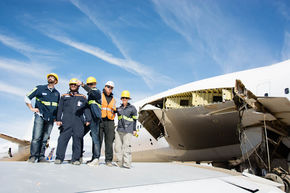
Aparte del desafío de perforar un material tan duro, el titanio requiere el uso de un flujo robusto y constante de lubricante / refrigerante para garantizar que el material salga del corte y que la broca / cortadora no falle prematuramente. La máquina de perforación magnética portátil MAB 485 tiene un sistema de lubricación interno automático que permite que un dispositivo de lubricación externo se conecte para suministrar líquido al sitio de corte. (Vea un video aquí que describe los desafíos del proyecto y cómo el MAB 485 se acercó a la reto).
Según Keru, cada corte a través de la pila completa de material tardó unos 12 minutos en completarse y se usó aproximadamente un medio galón de lubricante. Normalmente, los fabricantes pueden utilizar el depósito de aceite de corte integrado o aplicar lubricante manualmente. Sin embargo, con la necesidad de un alto flujo de refrigerante, una presión constante del taladro al material y los frecuentes cambios de orientación (vertical / horizontal / invertido), Keru diseñó un sistema de alimentación por gravedad de mayor capacidad para suministrar constantemente refrigerante al taladro, independientemente de de la orientación del corte.
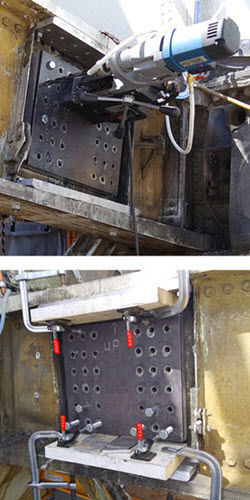
Para cortar los orificios, proteger el taladro y extender la vida útil de la herramienta tanto como sea posible, se especificó el lubricante de corte no tóxico ProLube ™. La fricción y el calor fueron los principales enemigos del proyecto: cuando se perfora titanio sin la lubricación suficiente, existe un alto potencial de endurecimiento inmediato de la pieza de trabajo, así como una chispa robusta y una posibilidad de riesgo de incendio. El lubricante Prolube ™ es eficiente, duradero y tiene una alta transferencia térmica; se mezcla con agua 16: 1 para la mayoría de las aplicaciones, por lo que solo se necesita una cantidad relativamente pequeña.
Afortunadamente, después de perforar los 232 hoyos, Keru informó que el motor y el cuerpo del taladro estaban en excelente estado y no mostraban signos de desgaste o estrés, debido a la perforación o las duras condiciones del desierto. El inteligente control electrónico de par de la máquina de perforación magnética equilibró la necesidad de alta potencia a bajas velocidades para atravesar el titanio de grado aeroespacial y minimizar la tensión en el motor.
“El MAB 485 de CS Unitec fue el equipo que marcó la diferencia al poder completar un trabajo de perforación difícil, afirmó Keru. "Las grandes cosas que lo hicieron funcionar fueron el motor de alto par, la elección de velocidades y el potente imán.”
Resumiendo el proyecto, Feldman no es más que orgulloso de su ejército de voluntarios, su dedicación y su inventiva con las herramientas disponibles. "Ellos (el Centro Espacial Johnson / Centro Espacial de la NASA Houston) hicieron que Boeing saliera y hiciera todo este trabajo con todas sus herramientas de lujo", recuerda Feldman. “¡Lo que tuvimos fue un Keru un CS Unitec hicimos lo mismo! El taladro Mag hizo toda la diferencia.”
Los taladros magnéticos eléctricos CS Unitec / BDS Maschinen se fabrican en Alemania.