Acabado de acero inoxidable: vale la pena aprender acerca de este arte
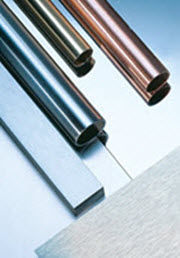
A medida que los arquitectos y diseñadores solicitan diseños más exclusivos y decorativos en acero inoxidable, la necesidad de que los fabricantes de metal comprendan y sean capaces de crear, combinar o duplicar estos diseños se vuelve cada vez más complejo. Para aumentar este desafío, las sutiles variaciones de los acabados comunes tradicionales hacen que no solo sea difícil identificar el acabado, sino que también es casi imposible duplicarlo utilizando métodos manuales. El ajuste, la forma y el acabado son ahora más importantes para los clientes, y ha pasado el tiempo de los fabricantes que producen simplemente un acabado "comercialmente aceptable". El acabado se ha convertido en una forma de arte, con fabricantes que luchan por aprender cómo lograr estos toques modernos de una manera rentable.
Este artículo identificará los acabados de acero inoxidable más comunes reconocidos por la industria de hojas metálicas: específicamente la SSINA (industria de acero especial de Norteamérica), además explicará cómo fueron creados por el fabricante y la mejor manera de replicar el acabado en el campo usando herramientas manuales.
Los grados comúnmente utilizados de acero inoxidable incluyen:
Serie 300 - aleaciones austeníticas de cromo y níquel
Tipos 301 a 309, el 304 es el que más se utiliza
Tipo 310 y 310S para aplicaciones de alta temperatura
Tipo 316 para usos alimenticios y de acero inoxidable quirúrgico, así como aplicaciones marinas y nucleares
Serie 400 - aleaciones de cromo ferríticas y martensíticas
Tipos 420 y 440 para aplicaciones de cubertería
Se proporcionan las definiciones de SSINA para cada acabado, seguidas de una explicación de cómo hacer coincidir el acabado, utilizando herramientas manuales en el campo, siempre que sea posible.
Acabado n.º 1
No. 1 Acabado es producido por acero inoxidable rodante que se ha calentado antes de laminar (laminado en caliente). Esto es seguido por un tratamiento térmico que produce una microestructura uniforme (recocido) y asegura que el acero inoxidable cumplirá con los requisitos de propiedades mecánicas. Después de estos pasos de procesamiento, la superficie tiene una apariencia oscura y no uniforme llamada "escala". El cromo superficial se ha perdido durante los pasos de procesamiento anteriores y, sin quitar la escala, el acero inoxidable no proporcionaría el nivel esperado de resistencia a la corrosión. La eliminación química de esta báscula se llama decapado o desincrustación, y es el paso de procesamiento final. Un acabado n.° 1 tiene una apariencia rugosa, opaca y no uniforme. 1
Como este acabado rara vez se utiliza en la fabricación, no hay forma de duplicarlo a mano sin quitar la "escala" y alterar la apariencia del acabado. Cualquier intento de eliminar la báscula con herramientas manuales en el campo cambiará el acabado por completo. No hay forma de duplicar el acabado n.º 1 con herramientas manuales.
Acabado n.º 2B
N.º 2B es un acabado brillante, laminado en frío comúnmente producido de la misma manera que el n.º 2D, excepto que el pase de laminación final con luz fría se realiza con rodillos pulidos. Esto produce un acabado más reflectante que se asemeja a un espejo nublado. La reflectividad del acabado puede variar de un fabricante a otro y de una bobina a otra, con algunas bobinas parecidas a un espejo y otras bastante opacas. El n.° 2B es un acabado laminado en frío de uso general que se utiliza comúnmente para todas las aplicaciones de embutición profunda, excepto las excepcionalmente difíciles. Se pule más fácilmente con un brillo alto que con un acabado n.º 1 o n.º 2D.1
El acabado 2B es el punto de partida más frecuente de la industria de fabricación y acabado para la fabricación de equipos petroquímicos y de fábricas de papel, tanques de hoja metálica y otros equipos en los que no se necesita ni se desea un acabado decorativo o lineal. Duplicar el acabado brillante y laminado en frío puede ser difícil debido a la variación en el acabado de un fabricante a otro y porque el acabado aplicado por el fabricante es muy uniforme y no presenta marcas en los rodillos. Cualquier intento de hacer coincidir este acabado mecánicamente a mano dará como resultado el cambio de la uniformidad del acabado base.
Acabado n.º 2D
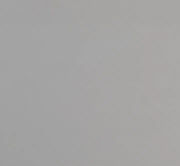
El n.º 2D es un acabado uniforme, gris plata opaco que se aplica a las bobinas más delgadas cuyo espesor se ha reducido mediante el laminado en frío. Después del laminado, la bobina se trata térmicamente para producir una microestructura uniforme (recocido) y para cumplir con los requisitos de propiedades mecánicas. Se requiere decapado o desincrustación después del tratamiento térmico para eliminar la capa superficial oscura sin cromo y restaurar la resistencia a la corrosión. El decapado puede ser el paso final en la producción de este acabado, pero, cuando la uniformidad y/o planicidad del acabado son importantes, hay un posterior pase final de laminación frío-luz (pase de revestimiento) a través de rodillos sin brillo. Se prefiere un acabado n.º 2D para los componentes embutidos profundos porque retiene bien los lubricantes. Se usa como sustrato cuando se desea un acabado pintado. 1
El acabado en 2D se usa con mayor frecuencia en la fabricación de sistemas de escape de la industria automotriz, bandejas, sartenes y artículos utilizados en plantas petroquímicas y sistemas de drenaje de techos. Debido a que este material está fabricado para retener líquidos, a menudo se usa cuando el material se pinta o utiliza donde no se requiere un acabado adicional. También es preferido por los fabricantes de metal como punto de partida para la fabricación antes de agregar un acabado decorativo o lineal sobre toda la pieza. Rara vez es necesario hacer coincidir el acabado de fábrica en las aplicaciones mencionadas anteriormente y cualquier intento de hacerlo da como resultado una superficie uniforme alterada por los abrasivos utilizados. Si se requiere un acabado n.º 2D, el mejor método es usar una herramienta de ángulo recto o de acabado lineal equipada con una rueda unificada de mayor tamaño de gravilla.
Acabado n.º 3
El acabado n.º 3 se caracteriza por líneas de pulido cortas, relativamente gruesas, paralelas, que se extienden uniformemente a lo largo de la bobina. Se obtiene puliendo mecánicamente con abrasivos gradualmente más finos o pasando la bobina a través de rodillos especiales, que presionan un patrón en la superficie que simula la apariencia de abrasión mecánica. Es un acabado moderadamente reflexivo. Cuando se pule mecánicamente, inicialmente se usan abrasivos de gravilla 50 u 80 y el acabado final se logra típicamente con abrasivos de gravilla 100 o 120. La rugosidad de la superficie es típicamente Ra 40 micropulgadas o menos. Si un fabricante necesita mezclar soldaduras o realizar otros trabajos de acabado, las líneas de pulido resultantes suelen ser más largas que las del producto pulido por un productor o una casa de pulido de peaje. 1
Este acabado se utiliza en la fabricación de equipos de procesamiento de alimentos que no tienen contacto directo con alimentos, además de equipos de cervecería y restaurantes. El fabricante utiliza rodillos para presionar el grano del recorrido en el acabado, produciendo un patrón lineal de grano corto. En el campo, un fabricante con una herramienta de acabado lineal de velocidad variable puede acercarse mucho a este acabado usando una cinta abrasiva con recubrimiento de cerámica de gravilla 50 a 80 de óxido o cerámica o una rueda de lámina a aproximadamente 3500-4500 RPM para establecer el grano, seguido de una cinta no tejida de vellón de gravilla 120 o tambor a 5000 RPM para suavizar el acabado y combinar con el acabado fabricado. El operador debe usar trazos cortos con la herramienta en un movimiento elíptico para duplicar el patrón lineal de grano corto del proceso de fabricación.
Acabado n.º 4
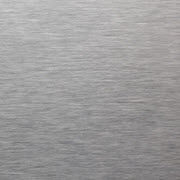
Acabado n.º 4 se caracteriza por líneas de pulido cortas y paralelas que se extienden uniformemente a lo largo de la bobina. Se obtiene puliendo mecánicamente un acabado N.° 3 con abrasivos gradualmente más finos. Según los requisitos de la aplicación, el acabado final puede ser entre gravilla 120 y 320. Los números de gravilla más altos producen líneas de pulido más finas y acabados más reflectantes. La rugosidad de la superficie es típicamente Ra 25 micropulgadas o menos. Este acabado de uso general es ampliamente utilizado para equipos de restaurantes y cocinas, escaparates y procesamiento de alimentos y equipos para lácteos. Si un fabricante necesita mezclar soldaduras o realizar otros trabajos de acabado, las líneas de pulido resultantes suelen ser más largas que las del producto pulido por un productor o una casa de pulido de peaje. 1
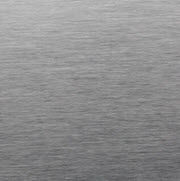
Este acabado es el acabado más popular para electrodomésticos, la industria de alimentos y bebidas, ascensores, escaleras mecánicas, hospitales y cualquier área de trabajo donde haya contacto con alimentos. Es el acabado favorito de los arquitectos y a menudo se clasifica como un acabado sanitario.
Crear este acabado en el campo es un proceso de dos pasos. El primer paso establece el rayado inicial utilizando una rueda de lámina o una cinta abrasiva con revestimiento entre 60-120 de gravilla, dependiendo del acabado existente. El segundo paso suaviza el rayón inicial y combina el acabado con el resultado final deseado. Las cintas unidas a un tambor inflable o expansible crearán un rayón más profundo que la rueda de lámina, pero cualquiera de ellas funcionará; generalmente se reduce a las preferencias del pulidor. La herramienta debe ser operada a aproximadamente 3500 a 4500 RPM, con solo un 5 a 10 % más de presión que el peso de la herramienta para permitir que el abrasivo funcione mejor. La variación de RPM también permite al operador marcar el rayón para que coincida mejor con el acabado fabricado. Lo mejor es mover la herramienta en un movimiento elíptico en lugar de recto hacia adelante y hacia atrás para evitar líneas de acabado notables. Al mover la herramienta de esta manera, el operador también corta las líneas de acabado lineales para que coincidan con las líneas de pulido más cortas hechas por el productor. El segundo paso, utilizando la misma herramienta y una cinta o tambor de vellón no tejido de gravilla 80-150, se suavizará y se mezclará en el acabado para que coincida con el acabado existente. Tenga en cuenta que RPM es más crítico en este punto. Cuanto más altas son las RPM, más reflectante es el acabado; cuanto más bajas son las RPM, más distintivo es el acabado. El sistema para acabado solo debe usar un ligero aumento en la presión por encima del peso de la herramienta para permitir una coincidencia suave y uniforme con el acabado de fábrica.
Este acabado puede variar sustancialmente de una pieza fabricada a otra y tendrá una dirección de acabado que debe tenerse en cuenta al tratar de fabricar dos piezas juntas o al intentar hacer coincidir el acabado existente en una pieza fabricada. Para determinar la dirección, el fabricante puede pasar la parte posterior de una uña por la pieza donde se dejará una marca en una dirección pero no en la otra. El fabricante debe asegurarse de colocar las hojas con la dirección del mismo modo para que el acabado permanezca uniforme y pueda combinarse después de la soldadura.
La soldadura puede necesitar ser mezclada con una herramienta rotativa y un disco de lámina de gravilla 80-120 usado con la dirección de la soldadura al espesor de 0.5 a 1 mm para evitar ahuecar los lados de la soldadura. Una vez que se mezcla la soldadura, el fabricante puede cambiar a una herramienta de acabado lineal con un tambor o una cinta para volver a engrasar el área afectada y establecer el rayón siguiendo el procedimiento enumerado anteriormente.
Acabado n.º 6
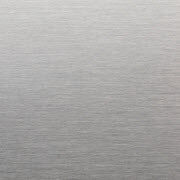
El n.º 6 es un acabado opaco, blanco plateado con líneas de pulido lineal relativamente cortas. Tiene una reflectividad menor que el acabado N.° 4. Es producido por el cepillado Tampico con una hoja de acabado N.° 4 en un medio abrasivo y de aceite. Este acabado se ve a veces en aplicaciones arquitectónicas de acero inoxidable que se instalaron aproximadamente entre los años 1930 y 1980, incluidos los paneles de columnas exteriores junto a las ventanas del Empire State Building. Ya no es producido por las innumerables casas de pulido, pero los fabricantes personalizados de vez en cuando lo aplican a proyectos pequeños. Otros acabados, que no se parecen en apariencia, a veces se venden como n.º 6. Debido a que este acabado ha dejado de existir esencialmente, no hay fotos disponibles. 1
Este acabado ha dejado de existir en el mercado como un acabado tradicional Nº 6, aunque un acabado satinado es frecuente y, a veces se identifica erróneamente como un acabado Nº 6. Para crear este acabado en el campo, el procedimiento y la técnica son los mismos que los del acabado estándar N.° 4, excepto que las gravillas que coinciden con el acabado son más altos. Comenzando con el material n.º 2B, el sistema para acabado usaría una cinta de gravilla 120-150 o un tambor en el sistema para acabado lineal para establecer el rayón y luego el acabo con un tambor no tejido fino o de lana de 180-220 o un cinturón fino. La velocidad de la herramienta sería la misma (aproximadamente 3000-3500 RPM) y la presión del operador debería permanecer un 10 % por encima del peso de la herramienta. El operador debe usar el mismo movimiento de pulido elíptico para garantizar el acabado lineal. Si se requiere una mayor reflectividad, el sistema para acabado puede cambiar a un tambor de gravilla 400 o una cinta superfina.
Acabado n.º 7
El acabado n.º 7 tiene un alto grado de reflectividad y una apariencia similar a un espejo. Un acabado n.º 4 que ha sido pulido con gravilla 320 se pulimenta por hasta 10 minutos, pero las líneas de gravilla existentes no se eliminan. Los restos de finas líneas de pulido generalmente pueden ser vistos por un observador parado a varios pies de distancia de un panel. 1
Acabado n.º 8
El n.º 8 es el acabado pulido más reflectante que está cubierto por las normas de ASTM. Se produce de la misma manera que el acabado n.º 7, excepto que el pulido se continúa durante cinco a 10 minutos adicionales. En comparación con un acabado n.º 7, las líneas de gravilla son mucho menos visibles, pero se pueden ver si el acabado se examina de cerca. El acabado resultante es similar a un espejo, pero no es un espejo perfecto. 1
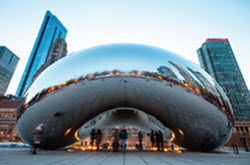
Estos dos acabados son acabados ornamentales generalmente utilizados donde hay poco contacto con fuentes externas debido al alto costo de mantener el acabado en el campo. Las aplicaciones incluyen paneles y columnas, a menudo en hoteles de lujo de alta gama y edificios de oficinas. Este acabado se está volviendo más y más popular. Un ejemplo es “Cloud Gate,” la escultura pública ubicada en Millennium Park en Chicago. Esta escultura, pulida con un acabado tipo espejo, es vista por millones anualmente y sirve como un punto focal para el turismo en Chicago.
El acabado tipo espejo no es difícil, pero lleva mucho tiempo. La diferencia entre el acabado n.º 7 y n.º 8 es solo un tiempo adicional de pulido; el procedimiento es el mismo. La diferencia entre el acabado reflectante de 10 pies a 2 pies a 2 pulgadas es en realidad un tiempo de acabado adicional, estimado en el doble por cada incremento de distancia descendente. Crear un acabado tipo espejo a mano requiere pasos de preacabado seguidos de pasos de pulido.
Preacabado
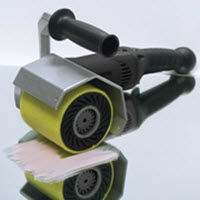
El preacabado se logra con el acabado con mangas o cintas de gravilla cada vez más altas, desde 320 hasta 2000, en un esfuerzo por aplanar la superficie y eliminar cualquier rayón. El sistema para acabado siempre debe “comenzar al final”, teniendo en cuenta el resultado final y sin arañar nunca la pieza de trabajo que será necesario quitar para lograr el acabado deseado. Esto significa que si la pieza de trabajo está limpia y sin rayones accidentales, es posible que el sistema para acabado no necesite utilizar los tamaños de gravilla más bajos porque hacerlo agregaría rayones innecesarios. En cambio, el fabricante puede comenzar el proceso con una mayor cantidad de gravilla, lo que evita la necesidad de eliminar cualquier rayón innecesario puesto en el material por las gravillas más bajas. Sin embargo, el fabricante no puede omitir los tamaños de gravillas una vez que se inicia el proceso, ya que cada tamaño de gravilla se utiliza para eliminar el rayón anterior.
La velocidad de la herramienta de acabado lineal está entre 3200 y 3700 RPM y la presentación cambia de la aplicación de grano en línea en los acabados lineales inferiores al grano transversal. Con cada cambio de gravilla sucesiva, el sistema para acabado debe cambiar la dirección de la herramienta entre 45 y 90 grados. Este cambio de dirección corta los rayones en trozos más pequeños, lo que permite que se eliminen más fácilmente y también nivela el material para aceptar el paso de pulido. Este paso es muy importante, cortar esquinas dará como resultado rayones restantes después del pulido. El operador debe utilizar el mismo movimiento de pulido elíptico para garantizar que el acabado lineal y el cambio de dirección entre cada cambio de gravilla sean igualmente importantes.
Pulido
El pulido es el último paso en el proceso de acabado del espejo. Implica el uso de compuestos sucesivos de “corte y color” con mangas de lana merino o de lana para pulir el material hasta la reflectividad deseada.
Paso 1:
Aplique compuesto para pulir con gravilla 1200 a 1500 sobre un manguito de pulido limpio, nunca directamente sobre el material, asegurándose de cubrir los bordes exteriores. El paso de pulido requiere varios minutos de movimiento multidireccional en un movimiento elíptico a una velocidad de 2500 a 3000 RPM para reducir los rayones cada vez más pequeños mientras se van eliminando. Continúe trabajando la pieza, agregando pasta adicional a la manga si es necesario hasta que la pieza parezca comenzar a brillar. Nota: el manguito de pulido debe estar marcado en el interior con el tamaño de gravilla o color del pasta para separarlo de otros manguitos, y debe colocarse en una bolsa que se puede volver a sellar limpia al retirarlo del rodillo impulsor para protegerlo de futuras contaminaciones.
Paso 2:
Se agrega un polvo de limpieza especial al área de la superficie para encapsular y eliminar el lustre antes de un segundo paso de pulido. Rocíe la superficie de trabajo con el polvo y luego use un paño limpio de microfibra para limpiar la superficie y prepararse para el siguiente paso.
Paso 3:
Aplique el compuesto de pulido de gravilla 2000 más alto en una nueva manga de pulido marcada. Repita el paso uno durante varios minutos, ya que el compuesto reduce aún más los rayones y pule la pieza para obtener un acabado de mejor calidad. Cuanto más tiempo pase en este paso, mayores serán las posibilidades de que se logre el acabado final.
Paso 4:
Una vez que se logra el acabado deseado desde el paso 3, espolvoree polvo de limpieza sobre la pieza nuevamente y luego quítela con un paño de microfibra. Tenga cuidado de eliminar el compuesto encapsulado sin agregar rayones a la superficie.
Paso 5:
El paso final usa una crema para pulir en un tambor de algodón para acentuar el acabado. El compuesto de pulido debe agregarse al tambor, no a la pieza de trabajo. La herramienta debe funcionar a toda velocidad y el operador apenas debe tocar la pieza de trabajo con el tambor de pulir. Este paso final dará como resultado un acabado tipo espejo altamente reflectante.
Lograr el acabado deseado no es complicado. Es simplemente una cuestión de entender el resultado deseado y seguir un procedimiento establecido, el sentido común y los hábitos de trabajo adecuados. El manejo adecuado de las herramientas y los consumibles es imprescindible para garantizar que el acabado coincida o se cree de manera adecuada y eficiente. Puede haber una gran satisfacción cuando el cliente final está entusiasmado con los resultados de una pieza de trabajo fabricada con el acabado exacto. Se parecerá a una obra de arte, porque eso es exactamente lo que es.
Para obtener más información sobre cómo los acabados superficiales mencionados arriba pueden lograrse de manera eficiente y exitosa, o para discutir cualquier problema técnico que pueda tener tratando de obtener los acabados antes mencionados, comuníquese con los expertos en acabado de superficies de CS Unitec al 1-800-700-5919 o al 203-853-9522.
Referencias:
1http://www.ssina.com/finishes/sheetsamples.html